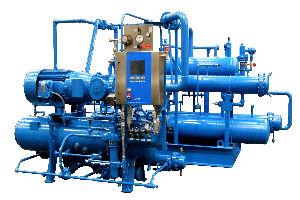
Por: Héctor Gómez Pérez
Muchas industrias: avícola, porcina, lechera y cervecera, solo por mencionar algunos ejemplos, requieren del agua caliente para llevar a cabo varios de sus procesos de producción o incluso para la limpieza al interior de sus instalaciones. Esta agua caliente la obtienen de una caldera utlizando gas o cualquier otro combustible.
En este proceso son muchos los ahorros que dichas industrias pueden percibir si obtienen el agua caliente a partir del calor producido en el condensador de los sistemas de refrigeración, en este caso los que utilizan compresores de alta presión o mono tornillo.
Para entender este proceso, Germán Robledo, gerente de ventas para Latinoamérica de Vilter, aceptó la invitación de ACR LATINOAMÉRICA. Con él nos dimos a la tarea de conocer los secretos detrás de esta forma de optimizar los recursos ya existentes para generar procesos alternativos.
El sistema
Según Robledo, una empresa que utiliza una caldera a gas para calentar agua para sus procesos industriales puede gastar US$ 523.950 al año, mientras que si utiliza una bomba de calor gastaría US$148.050 durante el mismo periodo de tiempo. Esto representa un ahorro de US$ 375.900 anuales, equivalentes al 71,7% de los gastos, una cifra nada despreciable.
Pero para entrar en materia no sobra recordar que una bomba de calor es un dispositivo que ejecuta un ciclo de refrigeración de manera opuesta, ya que mientras el sistema de refrigeración remueve calor, el dispositivo en cuestión lo agrega.
Las bombas de calor más conocidas en la industria son del tipo de compresión mecánica y de absorción; precisamente el ciclo de refrigeración invertido es la manera más conocida de la compresión mecánica. Este ciclo invertido está en la capacidad de calentar agua, glicol u otros medios como aceites y fluidos hidraúlicos.
En el sector residencial, estas bombas son utilizadas para calentar el aire de los sistemas de calefacción y el agua para duchas, baños y cocinas. En el ámbito industrial se utilizan para calentar agua a altas temperaturas u otros elementos que serán utilizados para el secado, germinación, calefacción, limpieza o pasteurización.
Los refrigerantes
Según lo explicado por nuestro invitado, lo que prima en la escogencia de un refrigerante para una bomba de calor es su punto de presión crítica, es decir, la presión máxima a la que se puede llevar el refrigerante en compresión. Este aspecto determina el uso que se le puede dar a un refrigerante, debido a que a una determinada presión le corresponde a su vez una determinada temperatura.
“Si sabemos la temperatura que estamos buscando, se puede determinar el refrigerante o el gas que se debe utilizar conociendo su presión crítica. En su mayoría se han utilizado freonos, pero con el paso de los días han entrado otros como el amoniaco, el CO2 o el agua e hidrocarburos como el propano o el butano. Los primeros generan problemas ambientales; el amoniaco, por ejemplo, tiene problemas de toxicidad, mientras que los terceros tienen problemas de inflamabilidad”.
Aunque se debe tener mucho cuidado con su manejo por la toxidad, el amoniaco es el mejor refrigerante termodinámicamente hablando según ASHRAE, IIAR y RETA. Entre las medidas cautelares se cuentan tuberías de acero y soldaduras más calificadas, lo cual equivale a un costo de inversión más alto. “Pero su desempeño es mucho más eficiente en Kw Vs dinero por tonelada de refrigeración. Además tiene un punto crítico muy alto lo que le permite ser usado en las bombas de calor para cualquier proceso”, explicó Robledo y añadió que lo único que lo ha limitado es que no era muy conocido o no existían compresores que pudieran manejar las altas presiones sin desgastarlos o incluso averiarlos.
Características y ventajas
Como ya se había señalado, con un sistema de este tipo se obtiene energía que se pensaba desperdiciar en la atmósfera y se comprime el gas del sistema de refrigeración hasta el punto que pueda calentar el agua de acuerdo con las necesidades particulares de cada industria.
Robledo explica lo anterior con un ejemplo en el que se necesita tener agua a una temperatura de 80oC en un sistema cuyo refrigerante sea el amoniaco: “En este caso el amoniaco se comprime desde 181.21 psig (196.91 psiA/13.51 bar = 35oC/95 oF) hasta 90oC de saturación (735.4 psig/ 750.64 psiA/51.75 bar). En este valor el amoniaco hará la transferencia de calor para calentar el agua a 80oC y, al mismo tiempo, condensará el amoniaco y lo entregará en forma líquida a 735.4 psig que luego será expandido para regresar al ciclo de refrigeración a 181.21 psig, todo en un ciclo cerrado”.
Así, aunque se continúa con el proceso normal de refrigeración, se utiliza el sistema para un segundo objetivo: aprovechar el calor de condensación y llevarlo a la bomba de calor para comenzar otro ciclo de compresión, pero de una presión más alta.
De esta manera se consigue un tratamiento eficiente, con menos consumo de potencia (HP/Kw) que satisface las necesidades de frío como de agua caliente para una planta industrial, por ejemplo, que de no tener una bomba de calor usaría determinada cantidad de combustible y una caldera que no solo generaría consumo de energía y gasto de dinero, sino problemas de contaminación ambiental.
El Compresor y el amoniaco
Ya se había dicho que el compresor indicado para una bomba de calor era el mono tornillo, y Germán Robledo explicó las razones de la siguiente manera:
“Dado su diseño interno y configuración geométrica, todas las fuerzas o esfuerzos axiales y radiales generados por el trabajo de compresión se anulan o se ponen en equilibrio, haciendo posible que los rodamientos seleccionados tengan una vida útil más larga. Al mismo tiempo, los orificios o vasos comunicantes en el rotor o tornillo del compresor, ponen en equilibrio ambas caras o costados del tornillo a un solo valor de presión o fuerza, logrando que sin importar la presión que se ponga en la succión sea la misma en el lado opuesto del rotor, anulando la carga axial o empuje axial, cosa que no puede lograr un compresor de doble tornillo o parejas”.
Señaló además que los compresores mono tornillo tienen guías deslizantes independientes, o sistema “Paralex” para el manejo de capacidad variable o volumen variable (Vi), que permiten la salida de gas de alta presión de manera más suave, en oposición a las guías que están montadas en un solo eje (típico del doble tornillo) que frenan la salida del gas a alta presión y que generan contra presión o contra flujo.
Al trabajar con amoniaco se reemplaza el combustible fosil, altamente contaminte para el medio ambiente, que se necesitaba para calentar el agua en una caldera, pero además se pueden calentar medios a temperaturas cercanas a los 100 oC, aspecto ventajoso sobre otros refrigerantes en los que la temperatura alcanzaría como máximo los 50 oC.
“Este es un tema viejo, pero poco desarrollado con el amoniaco porque antes no existían los compresores adecuados para trabajar con presiones tan altas. Las continuas restricciones para los freones harán que el amoniaco tome más fuerza y los desplace, sin contar con los vaivenes políticos de los países productores de petróleo que constantemente generan crisis energéticas y altos costos, además todos los días buscamos tecnologías que ahorren y usen bien la energía. Antes nos dábamos el lujo de quemar gas o diesel sin reparar en las consecuencias económicas y ambientales, ahora cuidamos más el medio ambiente y nos preocupamos más por el impacto económico”, remató Robledo.